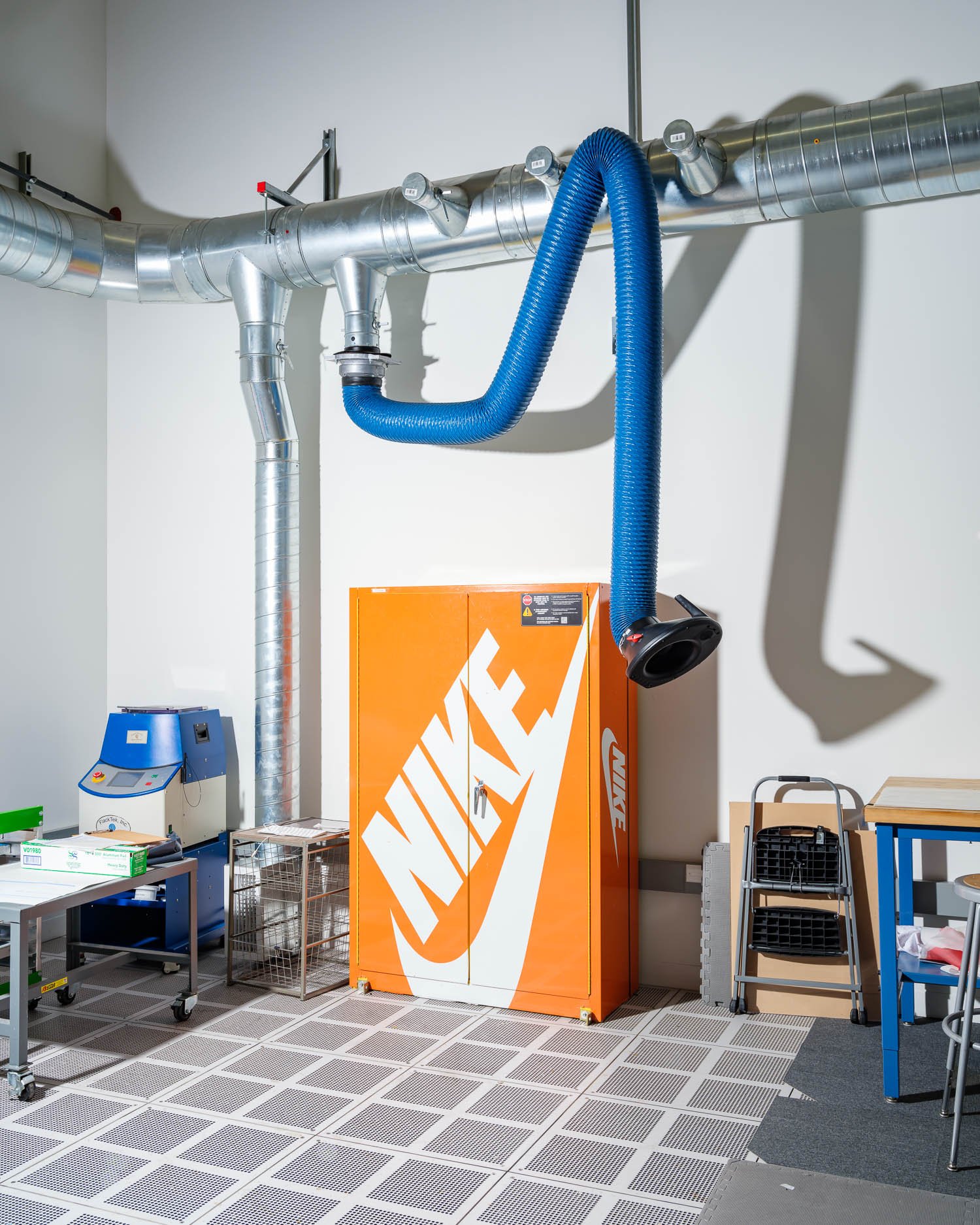
Nike invited me to photograph their archives, manufacturing and R&D facilities - and loads of other places photographers have never been - for a new exhibition and book about fifty years of Nike. It was an absolute treat.
The first ever museum exhibition about Nike, “Form Follows Motion”, is on show at the Vitra Design Museum near Basel from 20th September 2024 unitl 4th May 2025. The exhibition explores the company's five-decade ascent from a grassroots start-up to a global phenomenon. The focus is on Nike's design history, from the company's beginnings in the 1960s and the design of its famous “swoosh” logo, to iconic products such as the Air Jordan and Flyknit, and current research devoted to future materials and sustainability.
You can pick up the book at your local bookshop or direct from Vitra here.
Thanks to Sara Jhanjee and Nick Schonberger at Nike, and the best crew Mark Dexter and Edgar Salmeron. Exhibition curated by Glenn Adamson and exhibition design by Jayden Ali. Book design by Daniel Streat.
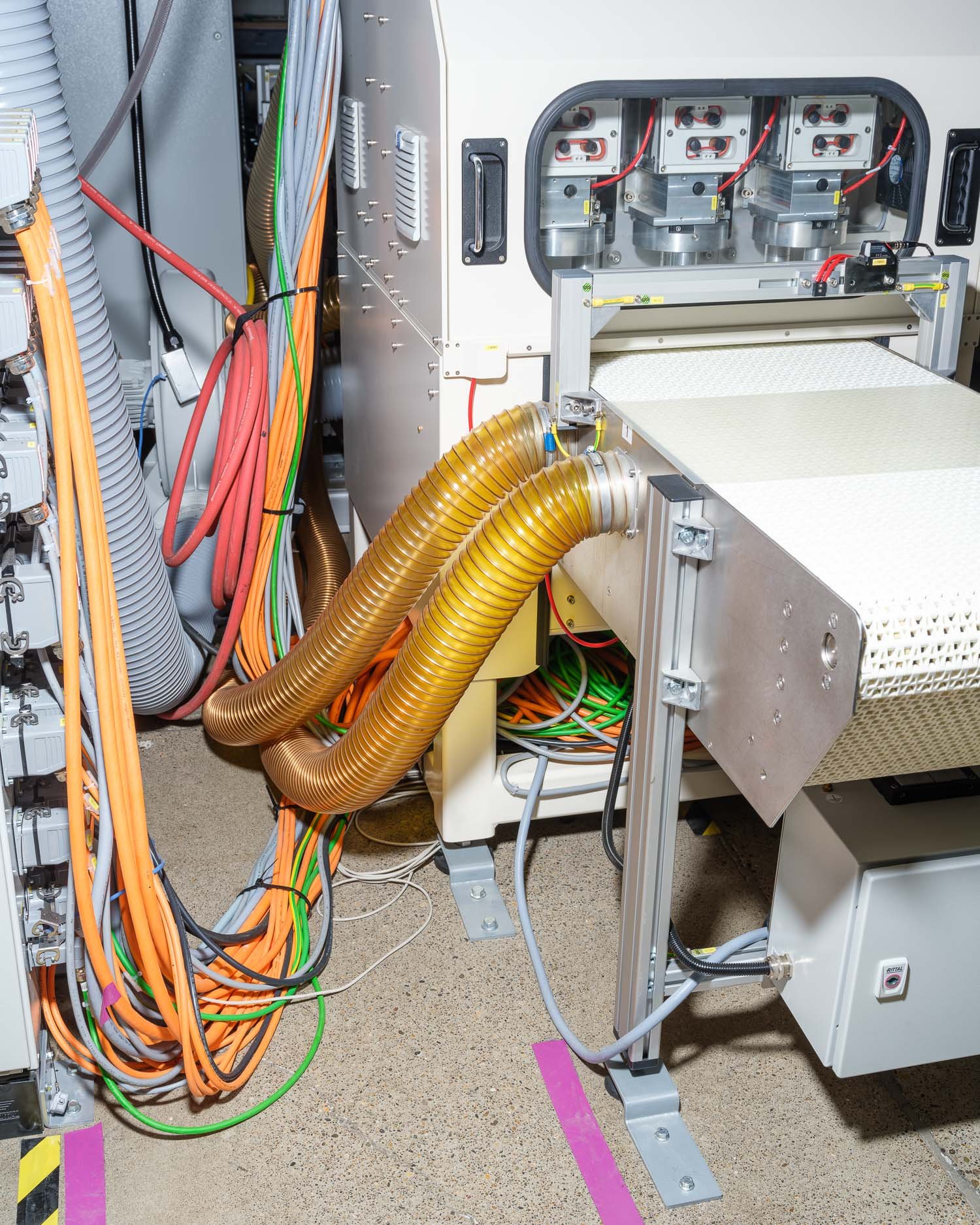
The Nike Advanced Product Creation Center (APCC), located at the headquarters in Beaverton, Oregon, is a top-secret state-of-the-art facility focused on innovation in product design. It’s a hub for rapid prototyping, allowing designers to quickly test and refine new ideas for shoes and apparel. By integrating advanced manufacturing techniques, the APCC streamlines the development process, reducing time and effort while pushing boundaries in sports innovation.

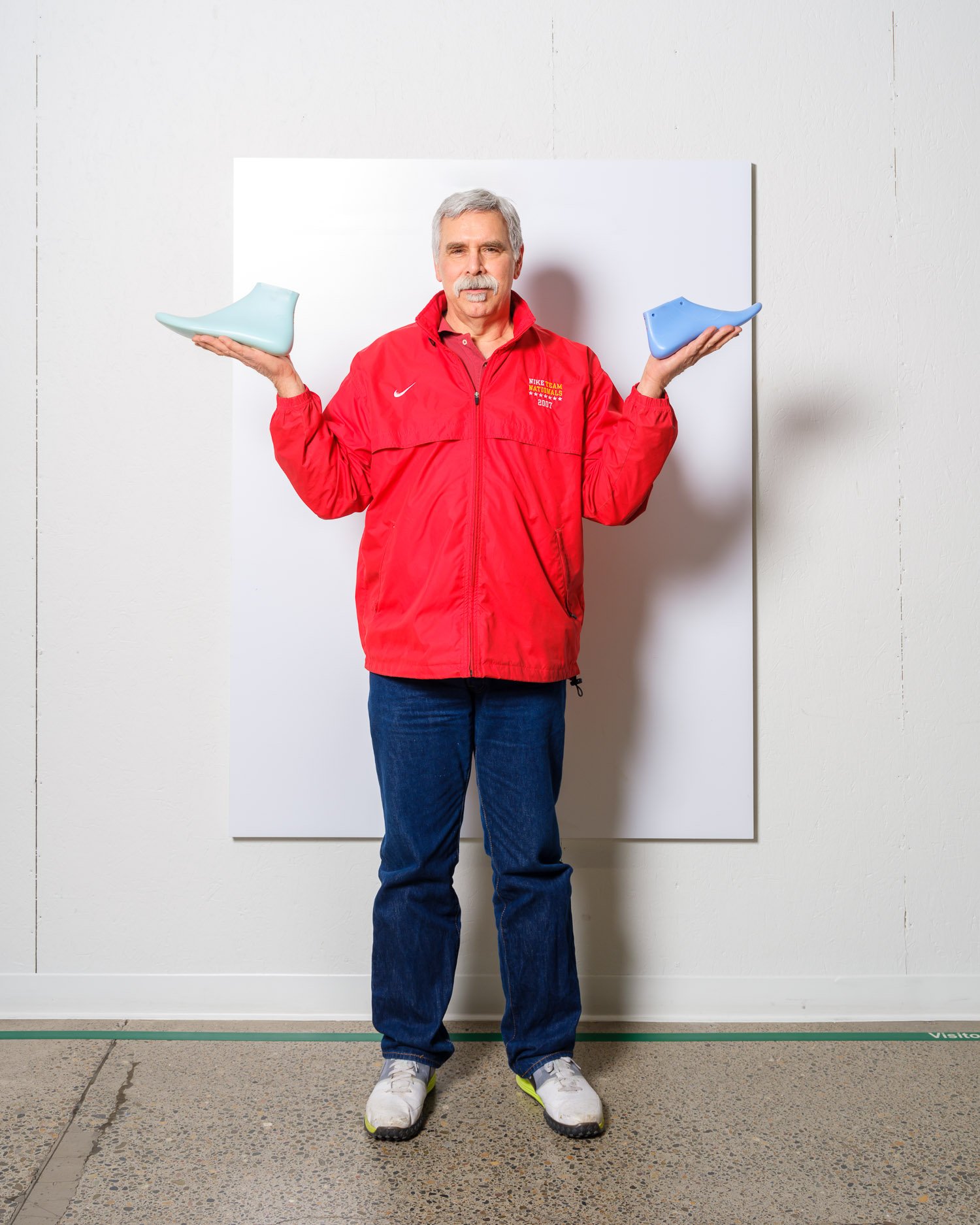
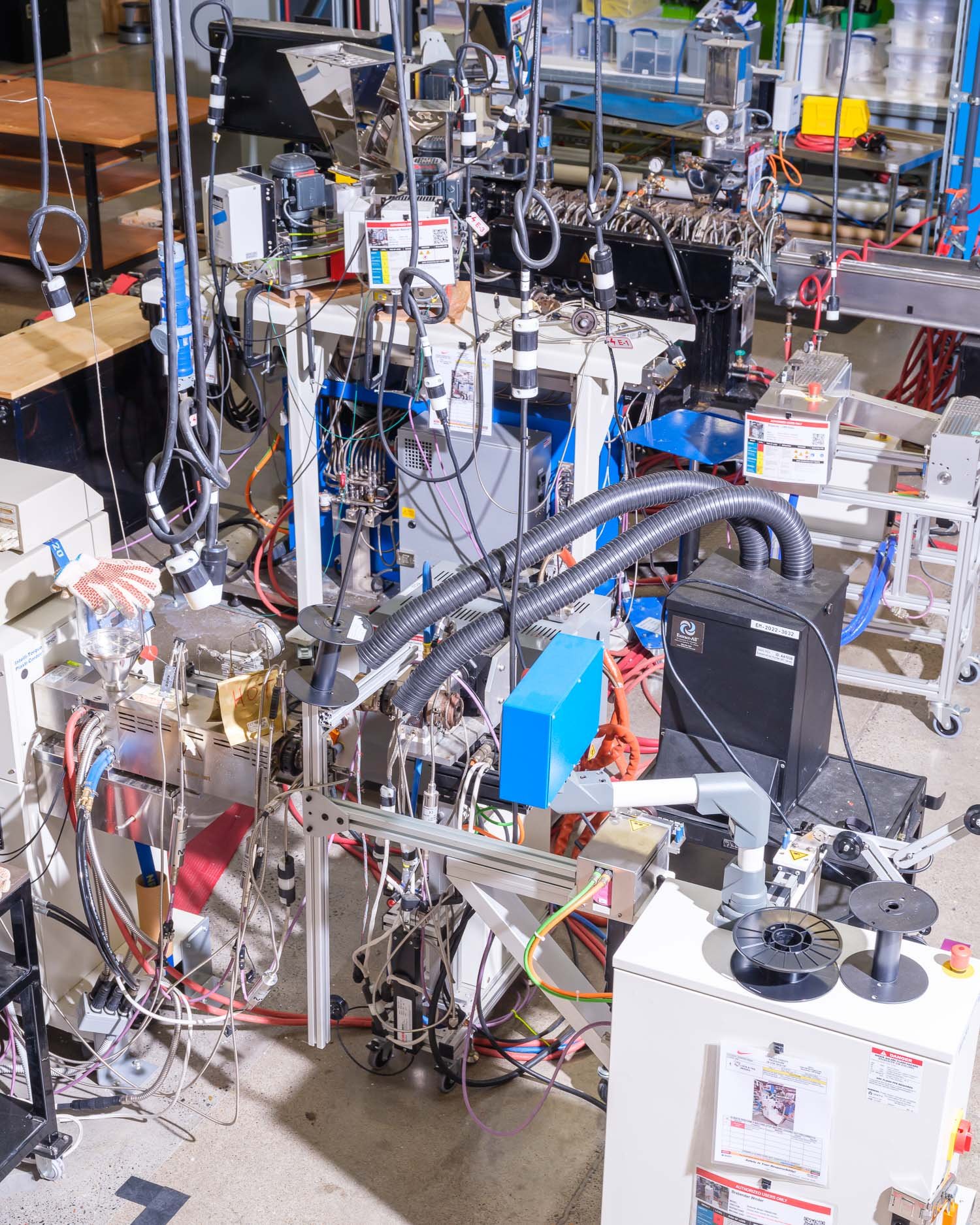
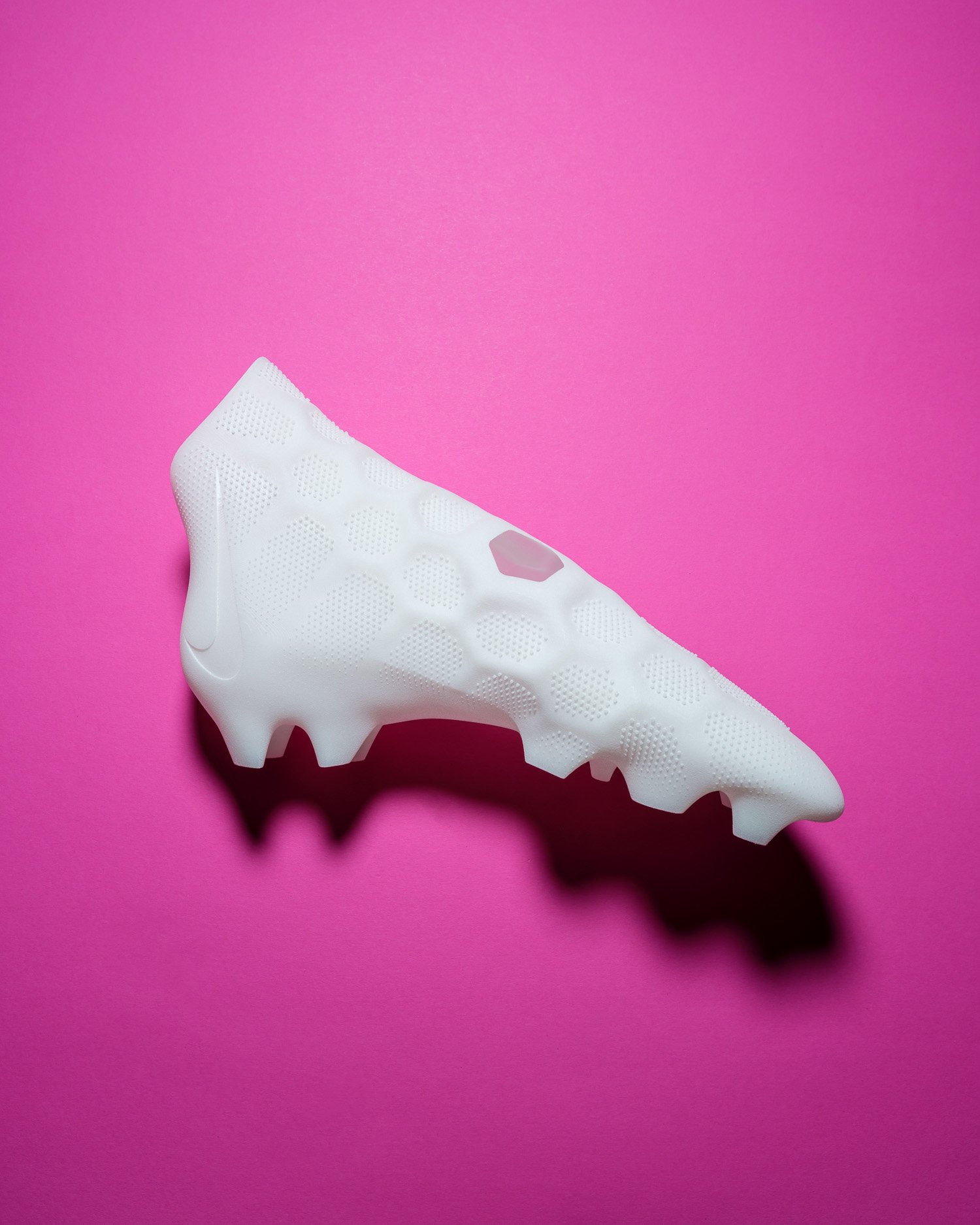
This 3D-printed prototype was created for and with Erling Haaland as one of 13 A.I.R. (Athlete Imagined Revolution) concepts Nike debuted in Paris in April 2024. The shape captures the curvature of the foot as it strikes the ball.
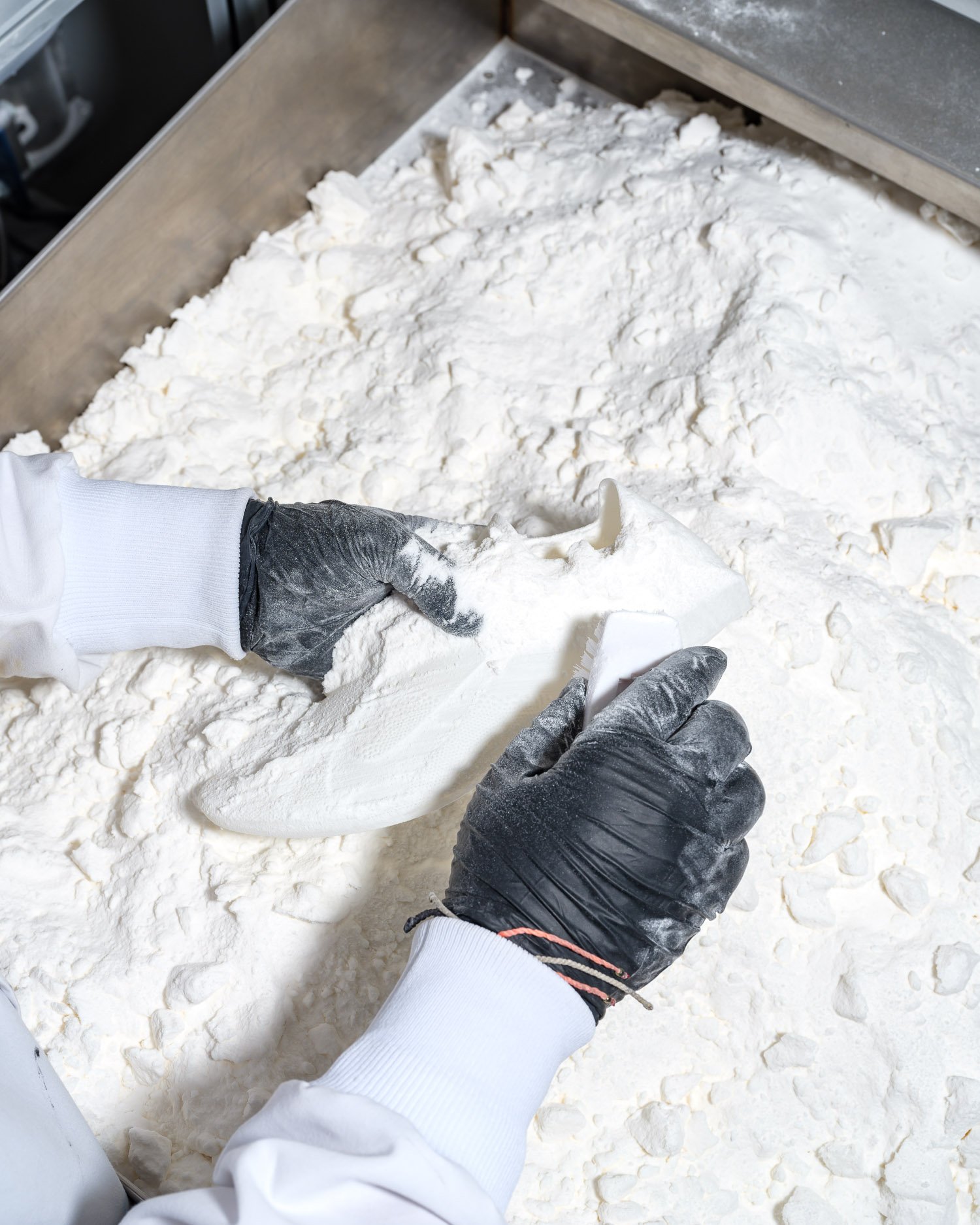
A technician dusts the powder off a freshly printed prototype in the Advanced Product Creation Center (APCC).
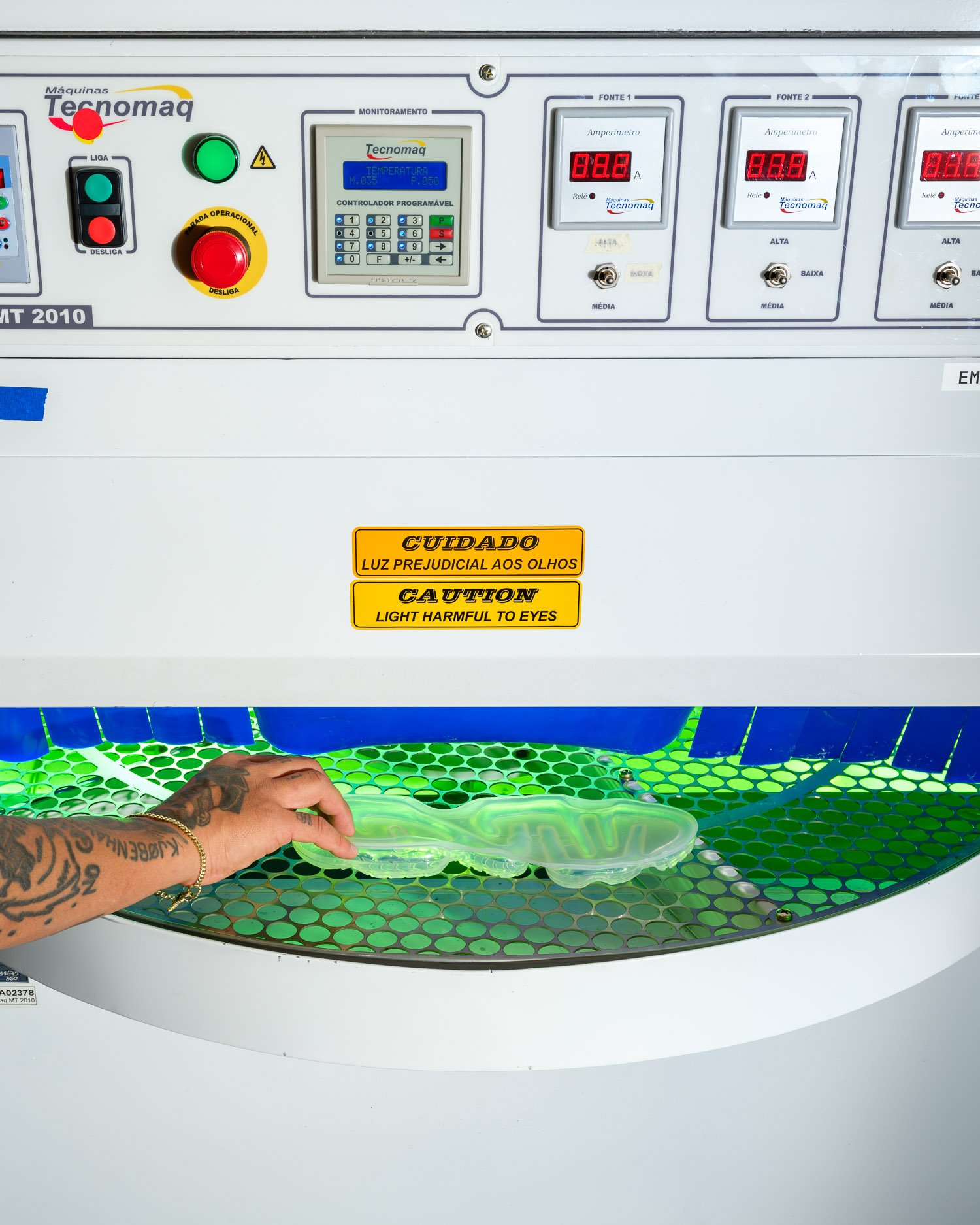
A UV oven cures a primed outsole in preparation for assembly in the Nike Advanced Product Creation Center (APCC).
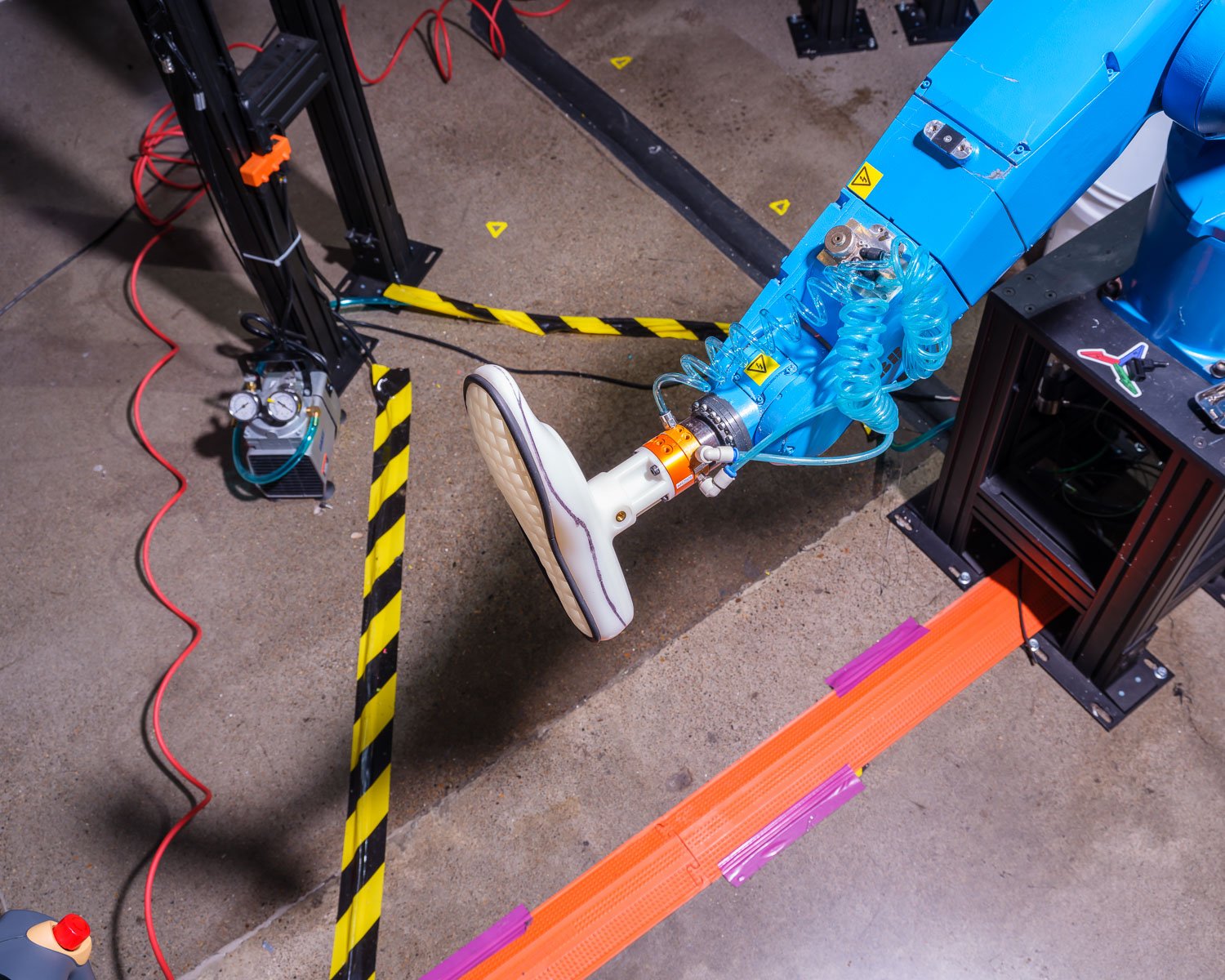
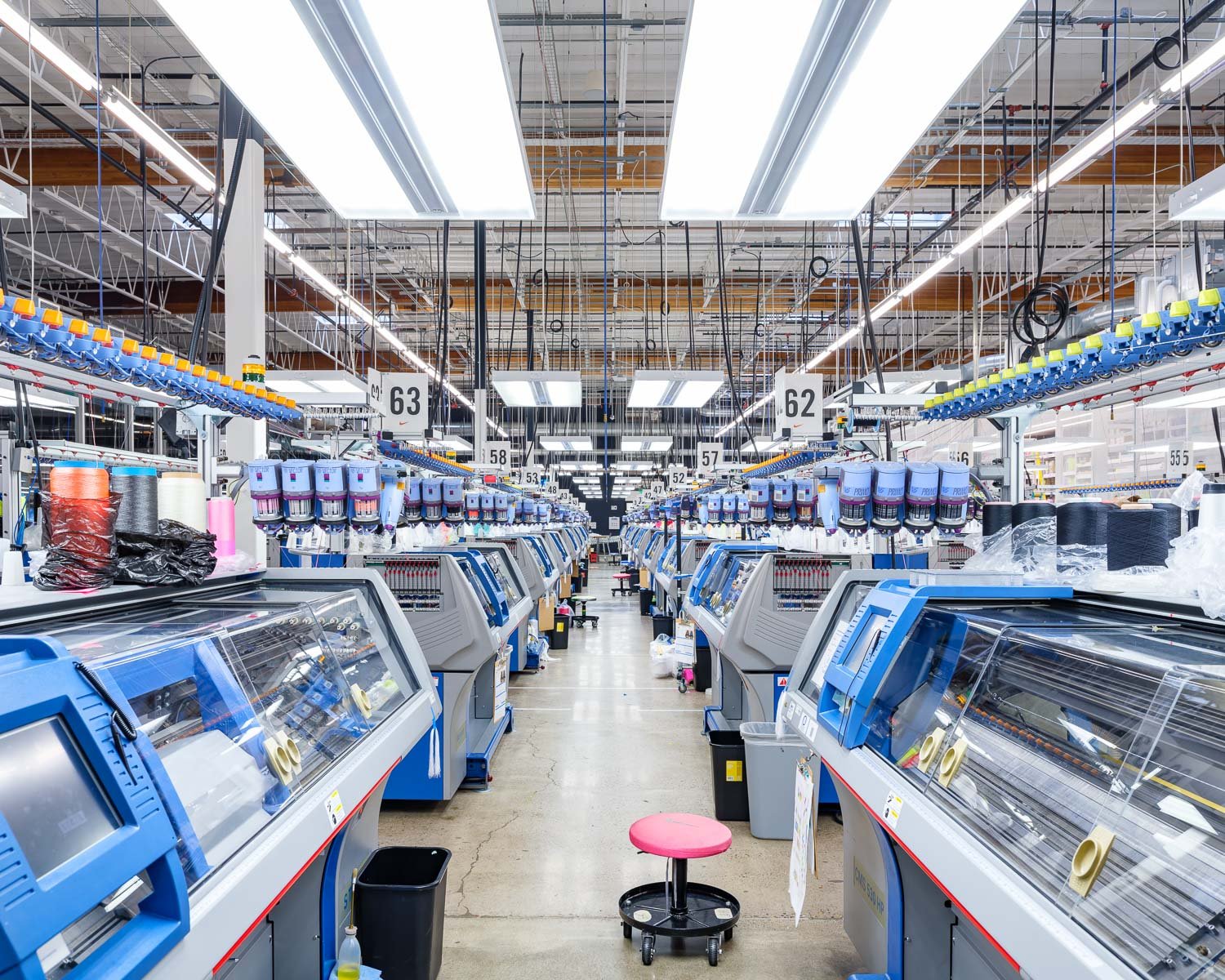

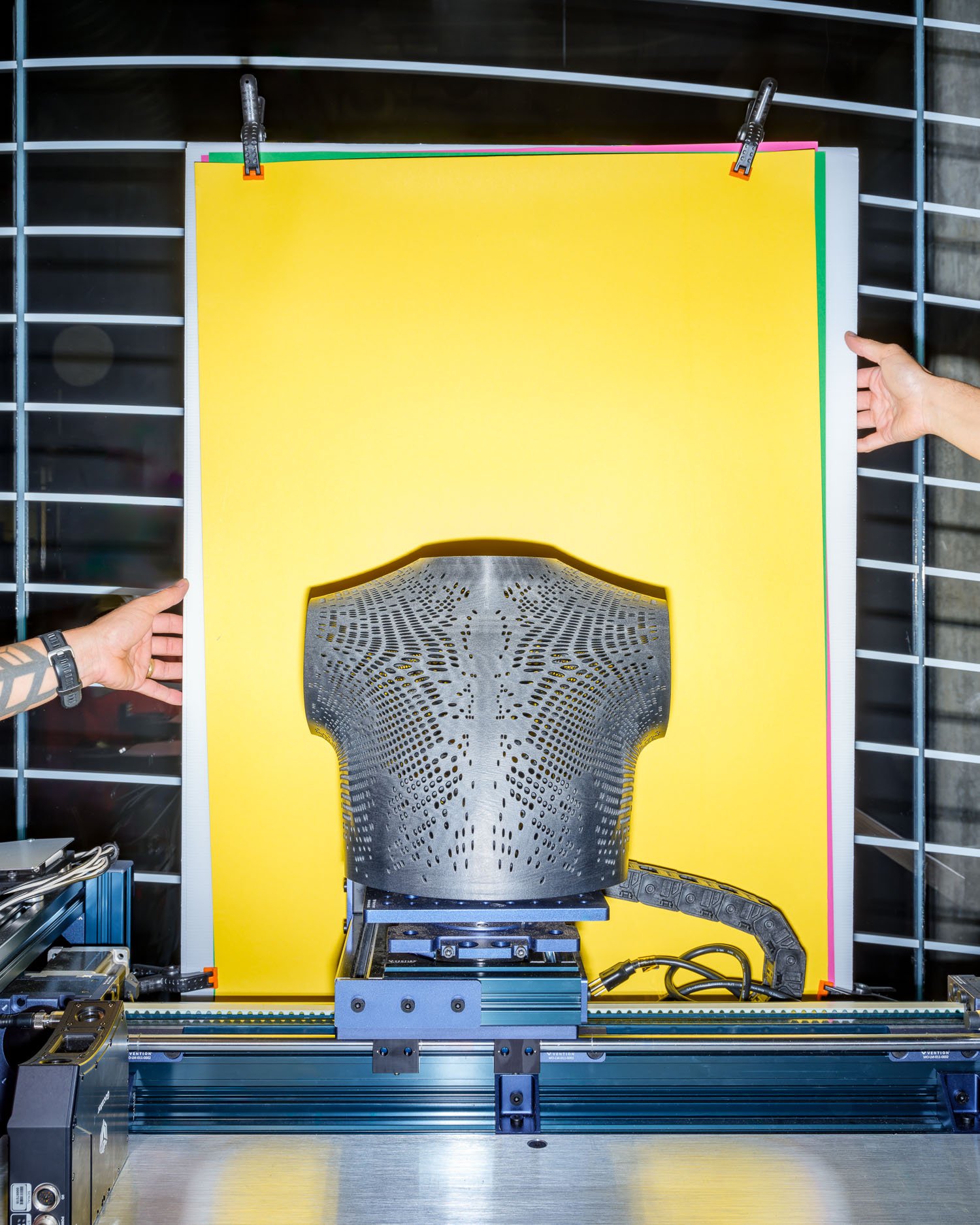
The LeBron James Innovation Center at Nike's headquarters in Beaverton, Oregon, is a cutting-edge facility focused on sports science and innovation. It houses the Nike Sport Research Lab (NSRL), where researchers, designers, and engineers work together to develop the future of athletic performance. The center is equipped with advanced tools like 400 motion-capture cameras, 97 force plates, and environmental chambers that can simulate various weather conditions to study how athletes perform in different environments.The facility features a full-size basketball court, a 200-meter endurance track, and even a 100-meter incline ramp, all designed to capture athletes' movements at full speed and under real-world conditions.

The vertical jump test is part of the baseline assessment for athletes at the Nike Sport Research Lab (NSRL). The stickers on the right show how high athletes like Michael Jordan and LeBron James can jump. It is insanely high!

To fully understand athletes, the Nike Sport Research Lab has incorporated mind sciences (sensory and cognitive tasks in the brain) as a growing area of expertise alongside biomechanics, exercise physiology, and functional anatomy.
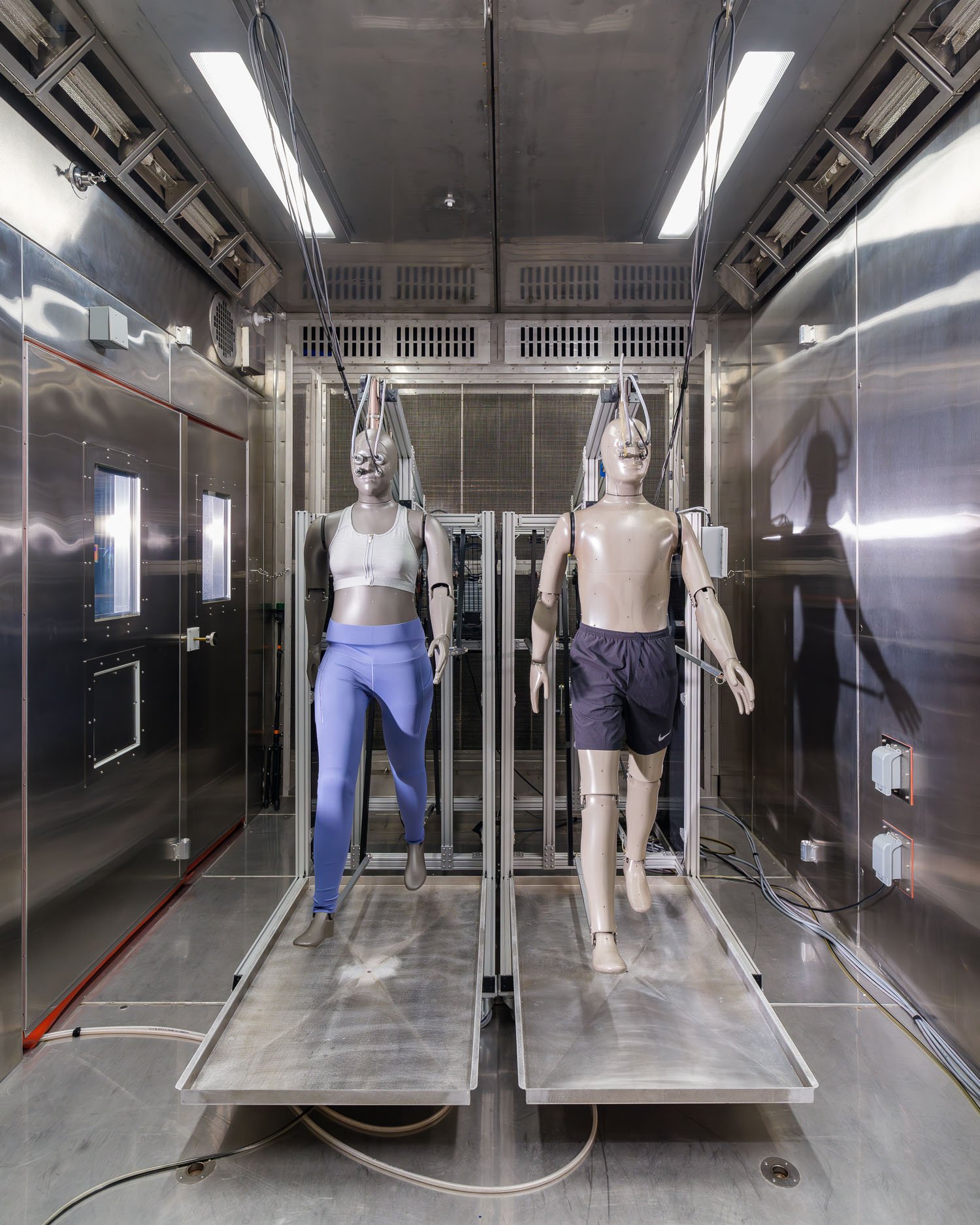
Mannequins that can move and sweat test different fabrics and garment designs.

Nike's LeBron James Innovation Center's last library includes the personal lasts of some of the greatest athletes of all time, including those of the building's namesake.

The Nike Air Manufacturing Innovation (Air MI) facility, plays a central role in the production of Nike's Air technology. Originally developed in the late 1970s, the Air Tailwind was the first shoe to feature Nike's air-cushioning system. This innovative cushioning was the result of collaboration between Nike and aerospace engineer Frank Rudy, who pioneered the concept of embedding pressurized air in a shoe sole to provide comfort and support. The facility in Oregon focuses on refining and manufacturing Nike's signature air units.

Nike Air Max Dn units ready to be inflated and trimmed. The Dn introduced Dynamic Air, with air flowing freely between two chambers. Each of the chambers (currently comprising two tubes each) is tuned to different air pressures: higher in the back, lower in the front.
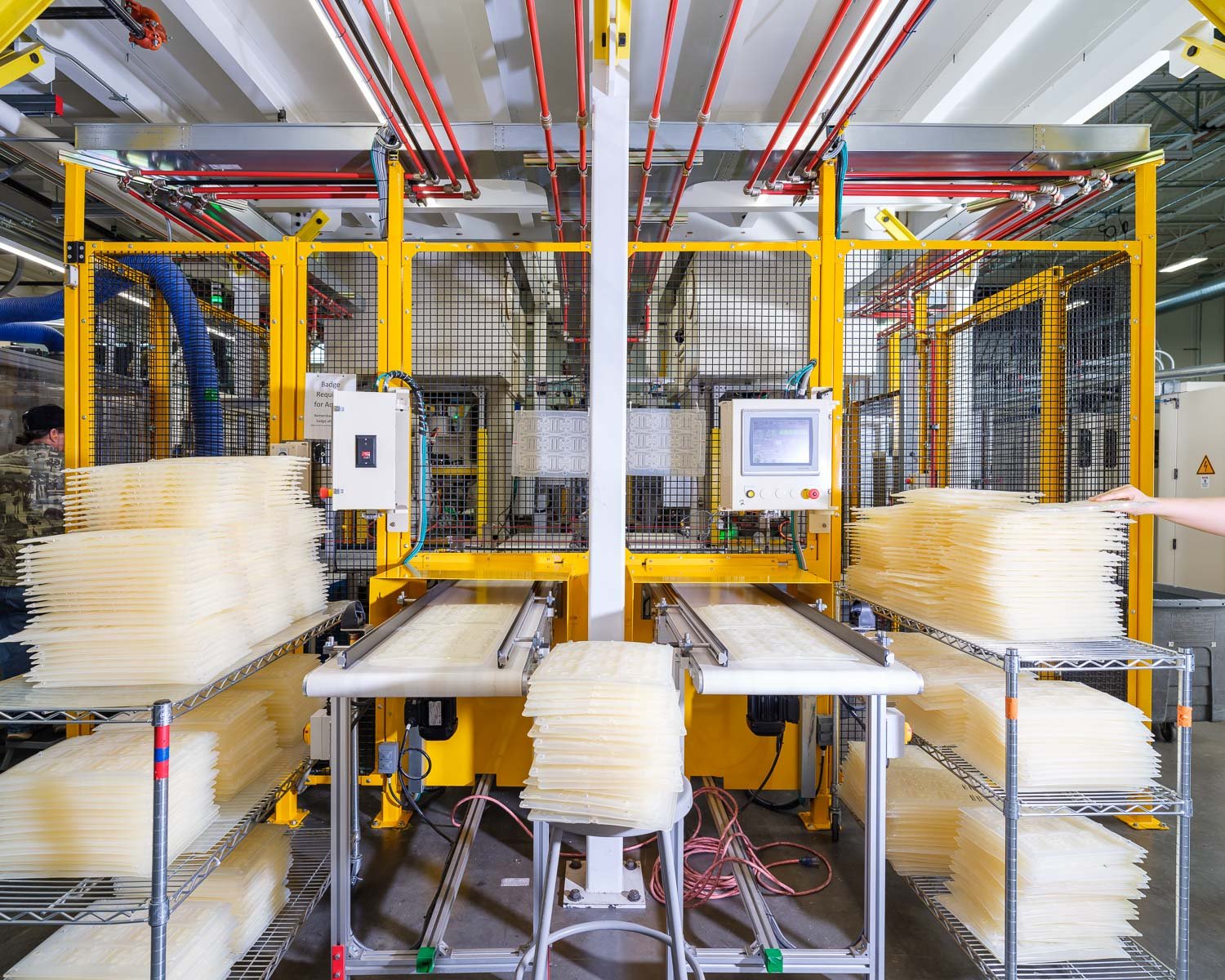

Nike currently holds over 500 patents on Air innovations.

The Department of Nike Archives (DNA) in Beaverton, Oregon, is a treasure trove of the brand's history, housing over 200,000 rare artifacts, prototypes, sketches, and memorabilia. This includes everything from the first Nike "Swoosh" design to early mechanical Shox prototypes, match shoes worn by Michael Jordan, Andre Agassi and Tiger woods, and much more. The archive is not open to the public, maintaining an air of mystery for years, but it serves as a key resource for Nike's ongoing design and innovation efforts.Shot for @nike for the book and exhibition "Nike: Form Follows Motion" at the @vitradesignmuseum

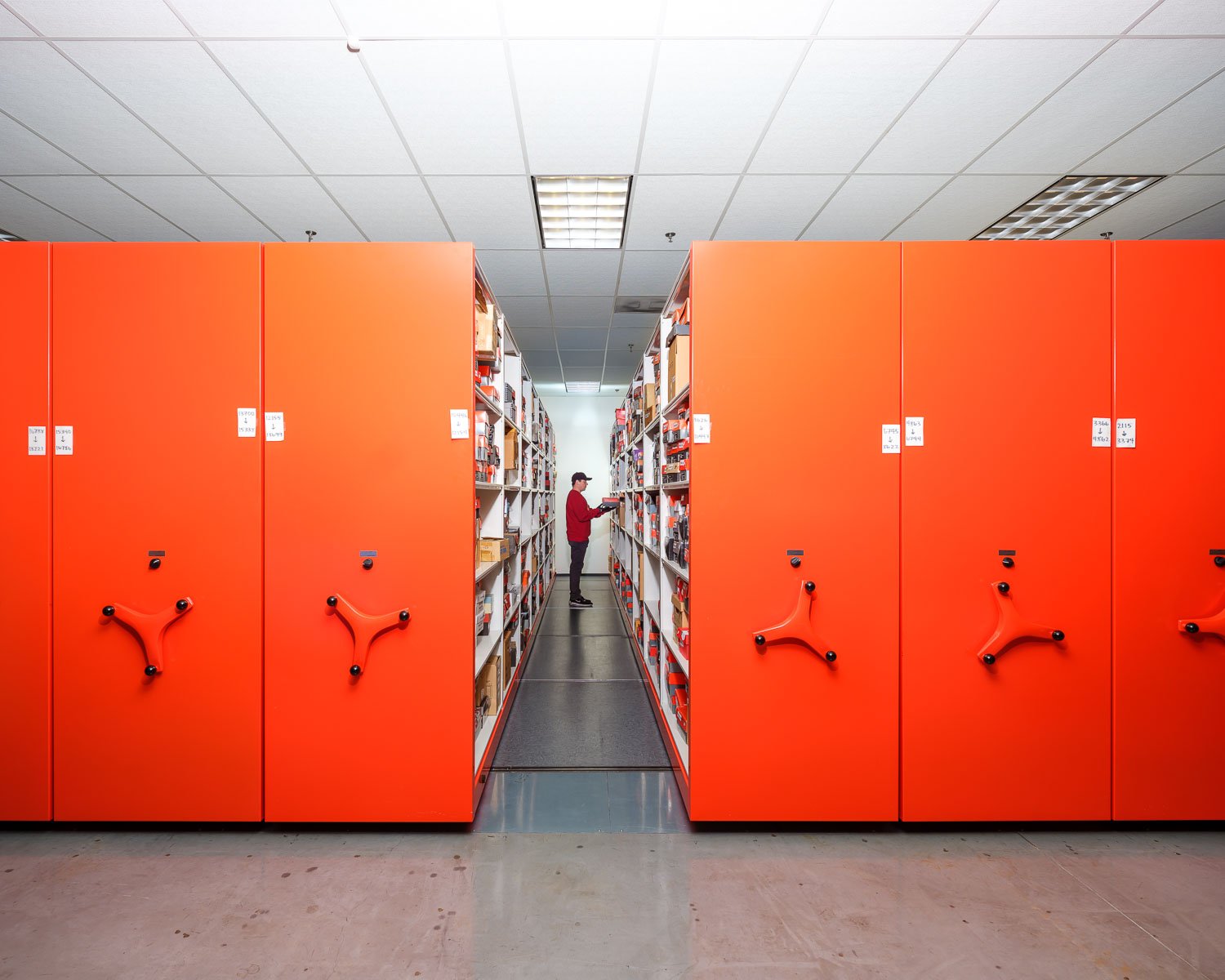
Racks of game worn shoes from Nike athletes such as Michael Jordan, Andre Agassi and Tiger Woods.

Andre Agassi game-worn shoes from the 90s.

The Nike Air Mag, designed by Tinker Hatfleld, was worn in the imagined year 2015 by Michael J. Fox's character in Back to the Future II. Nike later realized the idea of self-lacing shoes in 2016.
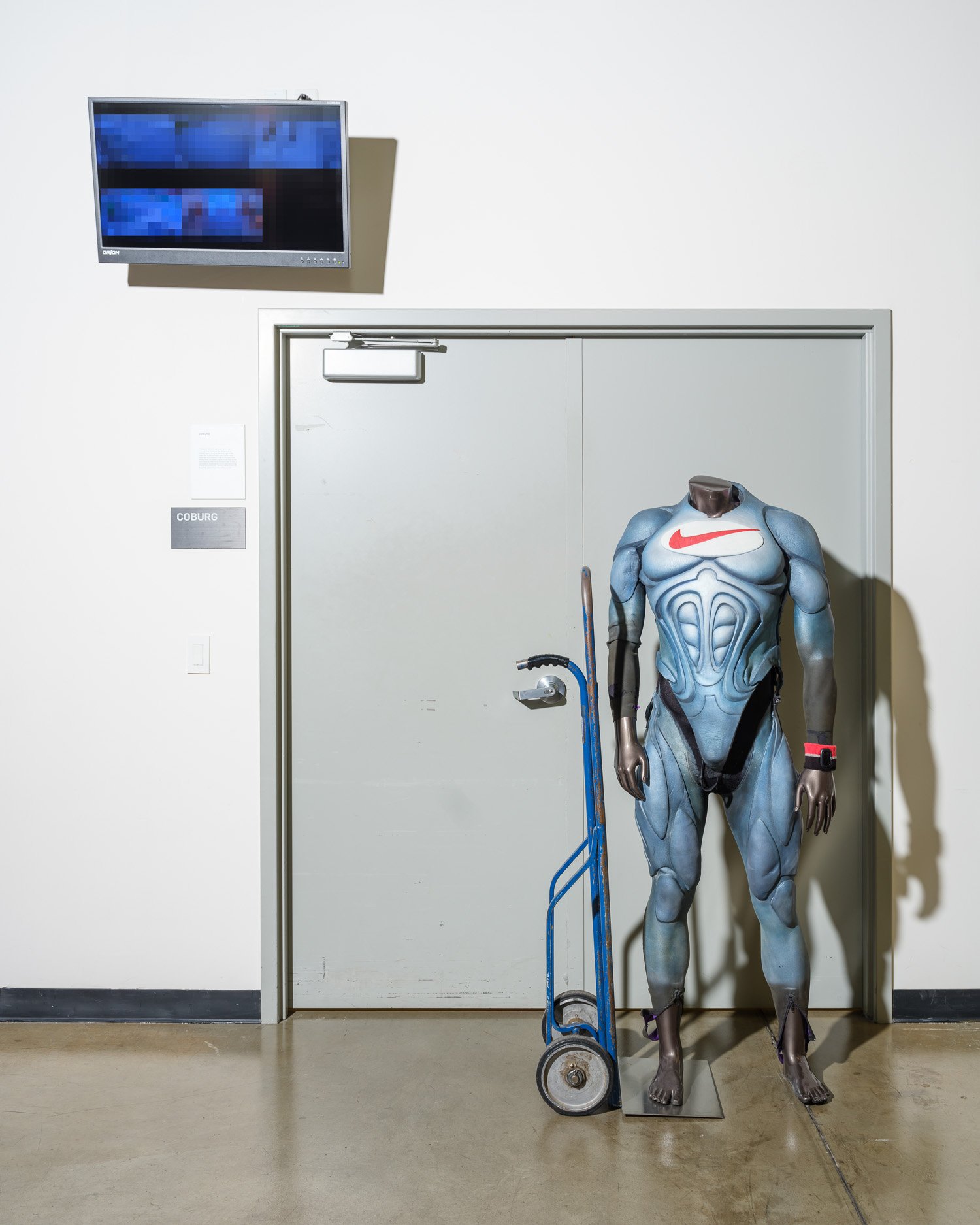
In 1996, Nike introduced Swooshman, a sports mascot. This neoprene suit was supposedly made by the same costume designer who was responsible for the Batman movies.


Headshots of Nike’s founder, Phil Knight.
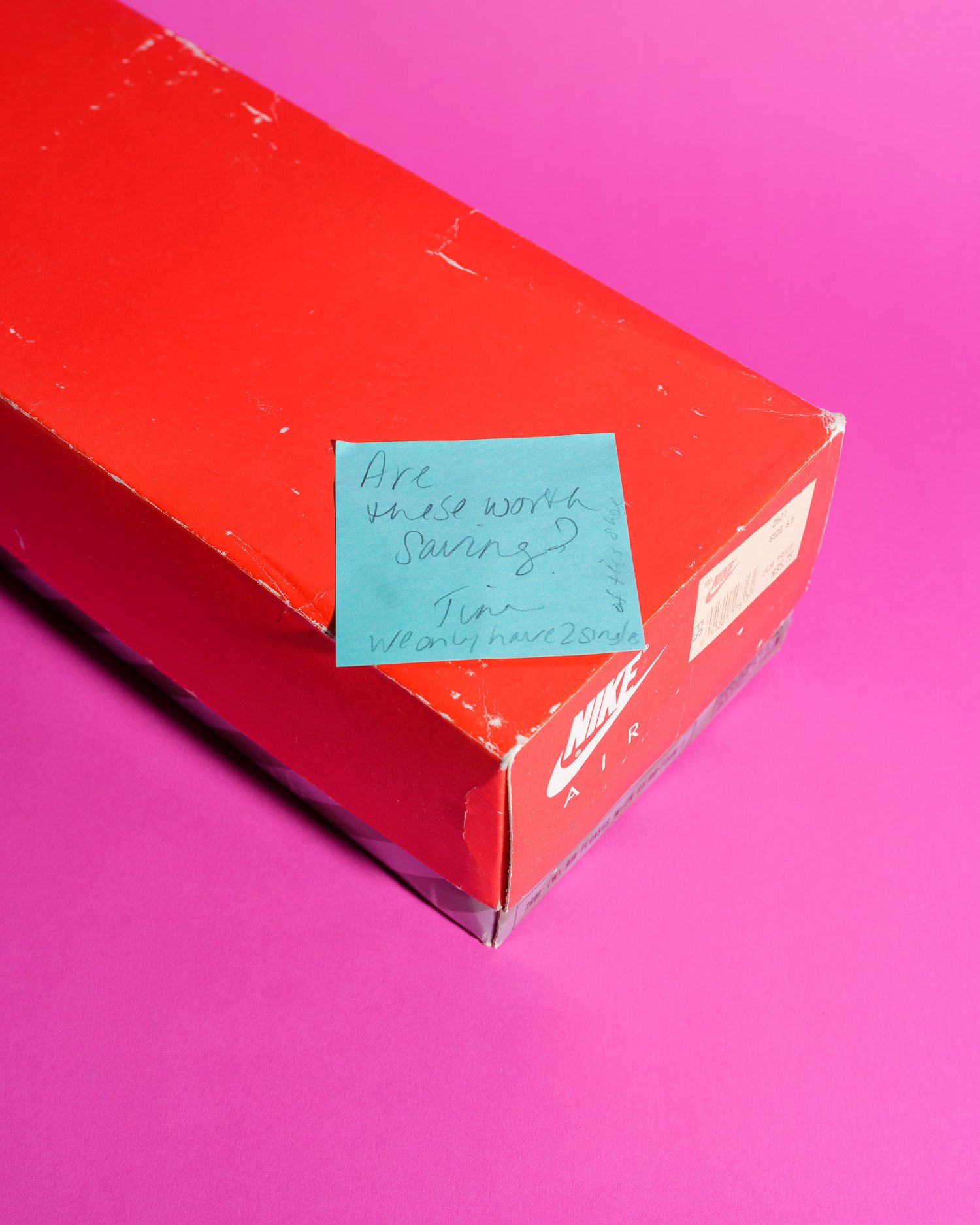
“Are these worth saving?”

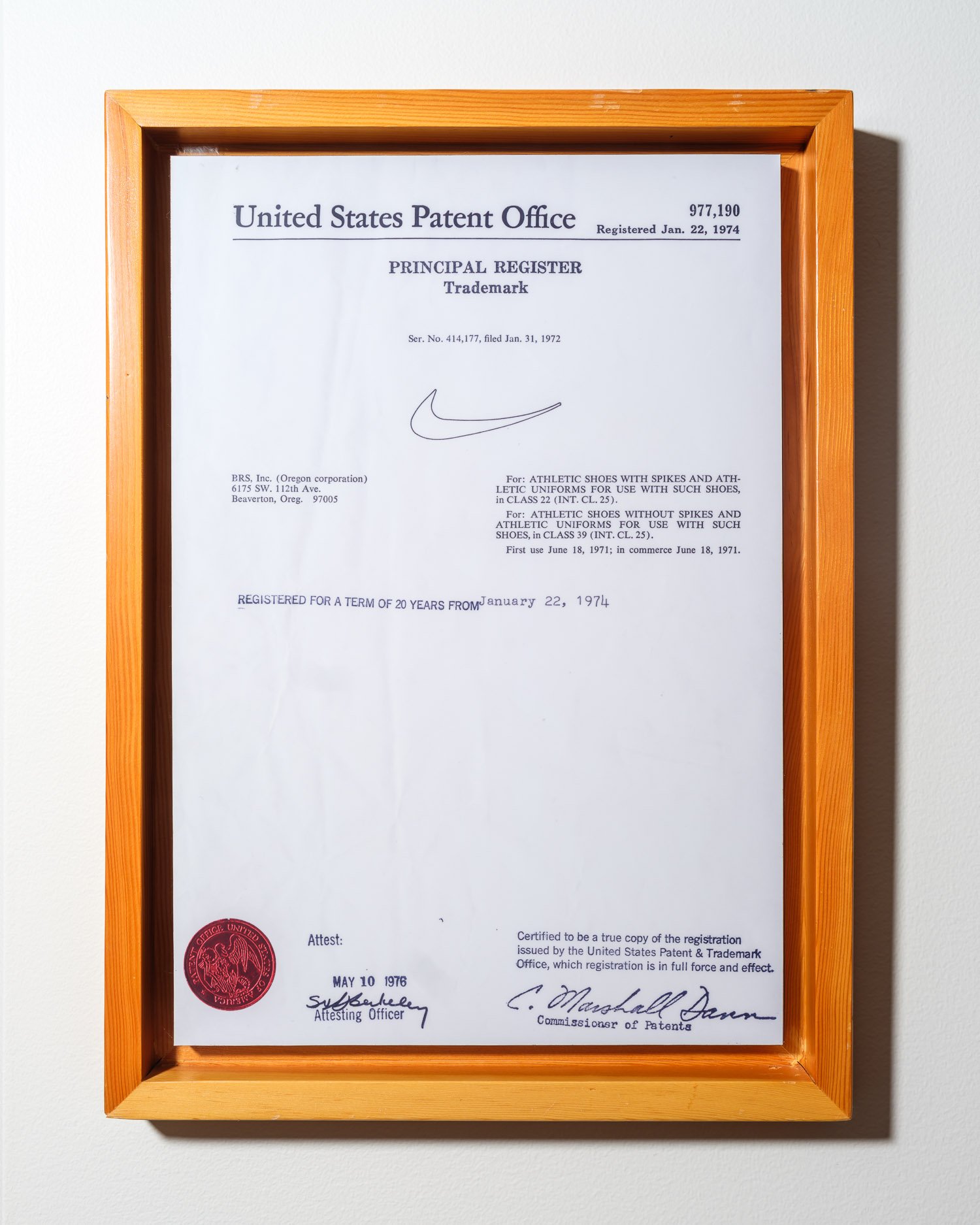
Filed in January 1972, the "Swoosh" trademark became officially registered in January 1974.
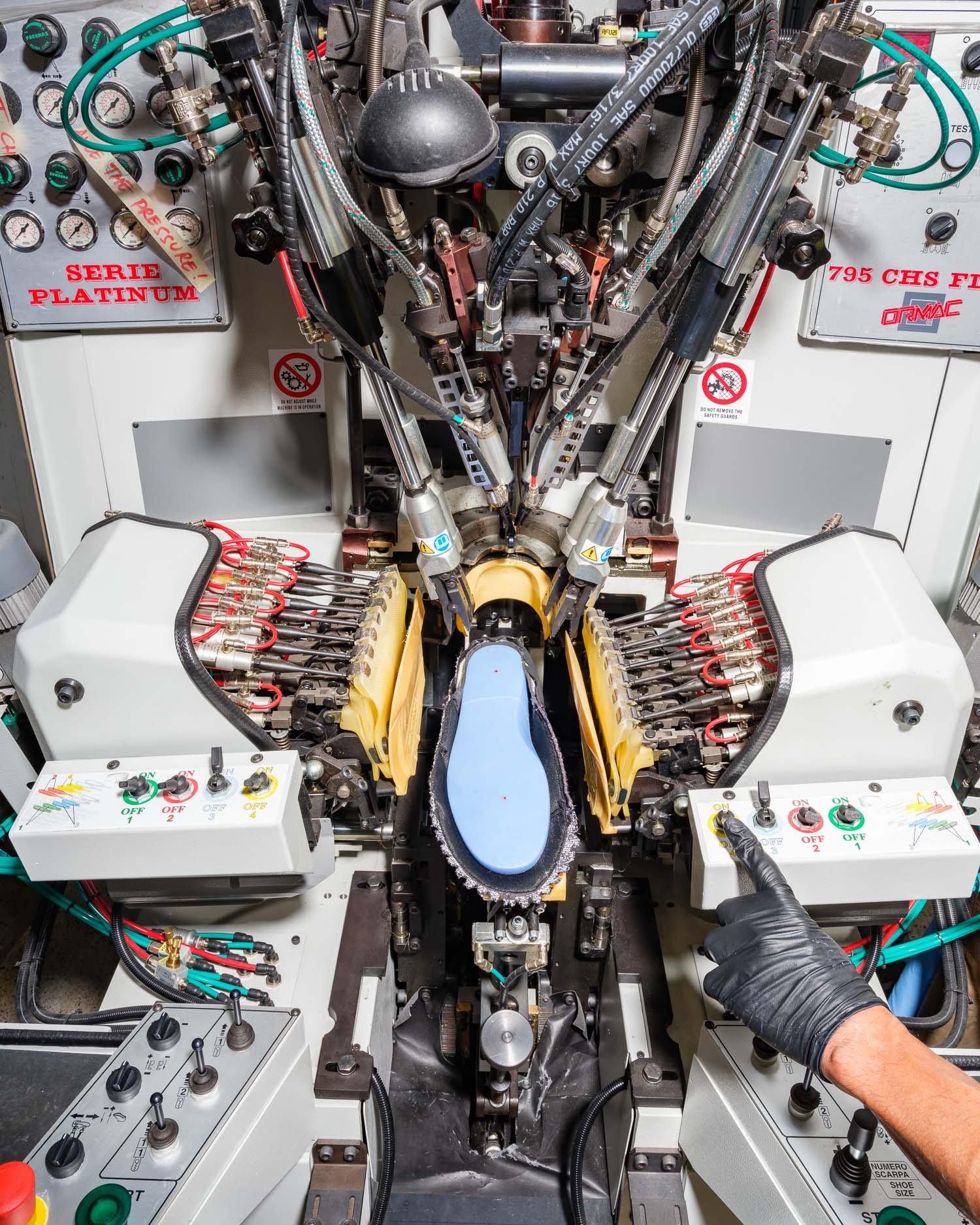
The Bowerman Foot Lab at Nike is a facility focused on developing and testing footwear innovations. Named after co-founder Bill Bowerman, it is located at Nike's headquarters in Beaverton, Oregon. The lab allows teams to quickly create and test new shoe designs using advanced prototyping machines. It’s a collaborative space where engineers, designers, and athletes work together to refine and improve performance, comfort, and durability of footwear.

Nike heel moulds in different sizes and shapes are kept chilled to aid in cooling material that's been moulded by heat and pressure.

Inside Nike's Bowerman Footwear Lab (BFL), a variety of polyurethane moulds are used to create midsoles from scratch. Here, the density of a new midsole is being tested by an engineer.

This device at Nike's Pegasus testing lab revolves continuously for days at a time to assess outsole durability.
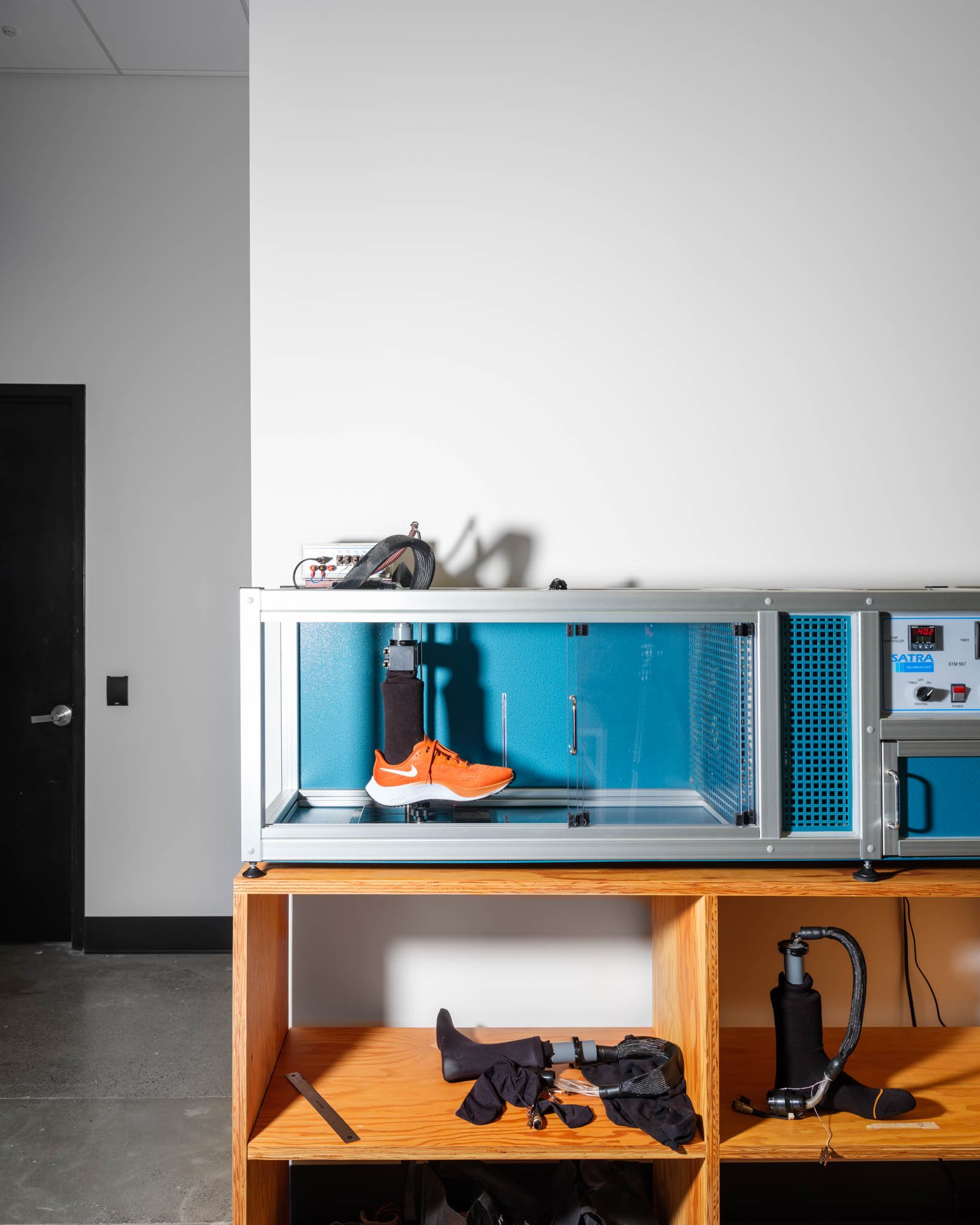
Along with breath-ability, this chamber assesses the thermal and moisture management offootwear at Nike's Pegasus Lab where products are tested.